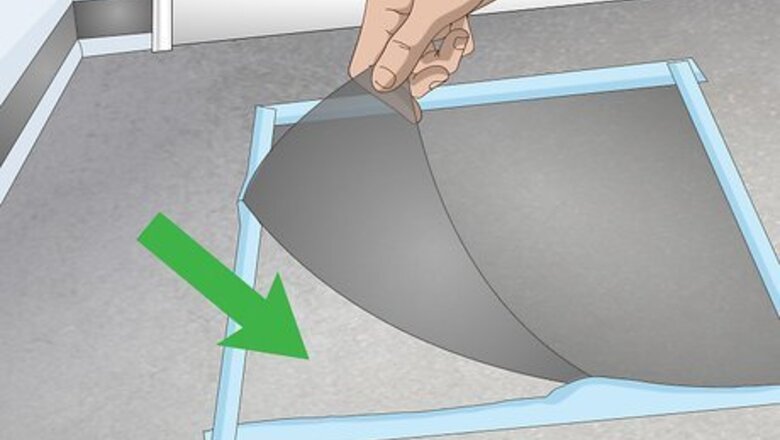
views
- Clean your floor by using a degreaser, hosing it down, sanding it with 180-grit sandpaper, and vacuuming up any remaining dirt and debris.
- Fill any cracks or holes with concrete filler and allow it to dry. Then, mix and apply an epoxy primer to your floor using a nap roller and let it dry for 12-24 hours.
- Use a nap roller to apply 2 coats of epoxy, letting it dry for 12-24 hours between each coat. Finish with a top coat if necessary.
Making Sure Epoxy is Suitable for Your Floor
Test your floor for moisture by taping down a plastic garbage bag. Place a plastic garbage bag on your garage floor and secure it with duct tape on all 4 sides. After 24 hours, gently lift up the corner of the bag to check for moisture accumulation. If the floor is dry underneath, you may proceed with your floor coating. If there is moisture, your floor is not suitable for epoxy—consider using a different floor coating, such as an acrylic sealant, instead. A floor with moisture present will cause the epoxy to adhere improperly and peel away.
Check if your concrete has been sealed by pouring water onto the floor. If the water immediately beads up, a concrete sealer has been used on your floor in the past. If this is the case, it is best to forego the epoxy project, as epoxy and concrete sealant are incompatible.
Wait at least 28 days before applying epoxy to a new slab of concrete. If you’re dealing with a newly installed concrete slab, wait at least 28 days (preferably 2 months) before applying the epoxy. This gives the floor time to cure and dry thoroughly prior to coating.
Remove any floor paint with sodium bicarbonate and a blasting unit. An epoxy coating will not seal properly if applied over polyurethane or latex floor paints. If your floor is covered in one of these materials, you must strip your floor with sodium bicarbonate and a blasting unit before starting the epoxy process. A blasting unit (pot blaster) works similarly to a power washer and is available for rent at a local hardware store. Rinse the floor thoroughly with clean water, let it dry overnight, and use an industrial vacuum to remove any remaining powder or debris.
Cleaning & Priming the Floor
Use a degreaser to remove oil and grease stains. Mop your entire floor using an industrial degreaser or solvent-based cleanser according to your product of choice’s directions. After you allow the floor to dry, look for any remaining oil/grease stains. Spot-clean these areas with a concrete degreaser and a stiff scrub brush. Then rinse the entire floor with clean water and let it dry overnight.
Sand the floor with a fine-grit sandpaper. Attach 180-grit sandpaper to a pole, hand, or floor sander. Slowly go over the entirety of your flooring, paying special attention to sand any rubber tire scuffs that may have accumulated on your floor. Finish by rinsing the floor with clean water and allow it to dry overnight. Floor sanders are typically available for rent at your local hardware store and make the sanding process significantly easier and faster.
Vacuum up any remaining cleaning products or debris. Use an industrial-strength vacuum to thoroughly suck up dust, leftover cleaning powder, and other dirt. Leftover debris can cause bubbles and imperfections in your epoxy coating, so be sure to remove it all to ensure that your floor turns out perfectly.
Use a pressure washer to deep clean the floor. Using an industrial power washer, spray down the garage floor so that any remaining impurities make their way out of the garage and toward a drain. Allow your flooring to dry out overnight. Vacuuming the floor with a wet vac after each time you expose it to water may be helpful in speeding up the amount of time it takes to dry, as well as removing fallen debris from the cleaning process. Pressure washers are available to rent from many home improvement stores or other rental outlets in your area. To avoid any potential damage to your flooring, use a pressure setting under 1,750 psi.
Etch the floor with muriatic acid. To etch the floor, you will need about 0.25 gallons (950 ml) of muriatic acid (a.k.a hydrochloric acid) for every 50–70 square feet (4.6–6.5 m) of the floor. Always follow the manufacturer’s instructions on your product of choice to ensure its proper application. General instructions for etching a concrete floor include: Thoroughly hose down the floor with water. Mix 1 part muriatic acid with 3 parts water in a plastic bucket. Use a plastic watering can or a pressure sprayer to coat the floor with the diluted acid. Finally, wait until the acid stops bubbling (between 2-15 minutes).
Neutralize and remove the muriatic acid with baking soda and water. Mix 8 fluid ounces (240 ml) of baking soda with 1 gallon (3,800 ml) of water. Apply this mixture over the floor to neutralize the acid. Some muriatic acid products will not need to be neutralized. Review your bottle's instructions to determine whether this is the case. You may also use water and ammonia in a 20:1 ratio to neutralize your flooring, though banking soda is considered safer, as ammonia is a harmful chemical.
Rinse the floor with clean water and leave it to dry overnight. Hose the floor down with clean water to rinse any remaining acid and neutralizer into the nearest drain. Be sure to let the floor dry out overnight before continuing the epoxy process.
Patch any cracks with an epoxy crack filler. After the floor is completely dry, examine it for cracks. Cracks that are 0.25 inches (0.64 cm) or larger, as well as any holes or spalled areas, will need to be filled in with epoxy crack filler. Place the product into the opening of the crack or crevice, then use a putty knife to scrape it down to surface level and smooth it out. Let the epoxy crack filler dry for 4-6 hours.
Choosing & Mixing an Epoxy Product
Choose between solvent-based or water-based epoxy. Solvent-based epoxies adhere well and are available in many colors. The drawback is that these products are extremely hazardous. Water-based epoxies are clear in color and don’t produce hazardous fumes, making for a safer application process. Both products typically contain 40-60% solids (epoxy). The higher the percentage, the harder your floor will be and the more expensive the product will likely become. Using a ventilator while applying solvent-based epoxy products is mandatory.
Buy an epoxy primer if your floor has cracks and holes. Epoxy primers smooth out minor imperfections in the floor and give the epoxy a better base to bond to. Additionally, primers add strength and durability to any floor. Primers must be used on porous, flaky, chalky, or rough floors. Always select a product compatible with the epoxy you plan to use.
Purchase enough epoxy for 2 coats. For a 450 square feet (42 m) garage (a typical 2-car garage), you will need 2–3 gallons (7.6–11 L) of epoxy per coat. This amount can vary based on the percentage of solids in the epoxy you buy, so be sure to check the labels to guarantee you've purchased the correct amount. Purchase enough epoxy to cover your floor in at least 2 coats. Solvent-based epoxy products are more challenging to find. While some paint specialty stores may carry them, you may need to visit an industrial-supply store. Water-based epoxy products can be purchased at most home supply stores.
Reduce hazards by wearing protective gear and turning off the power. Gloves, eye protection, a respirator, and rubber boots are essential while epoxying to keep you safe from harmful chemicals. Additionally, be sure to turn off gas/power to any water heaters or other appliances in the garage. Keep children and pets away from the area during application and drying, and run a ventilator throughout the entire process.
Applying the Epoxy
Use a ⁄4 inch (1.9 cm) nap roller to apply the epoxy primer. Dip your roller into the bucket, and spread a thin layer of epoxy primer onto your floor, starting at the back corner of the room and working your way toward the exit. Avoid letting the roller get too dry to ensure the epoxy application stays smooth and seamless. Using an extension handle on your roller may simplify the application process. Remember to wear a respirator and keep the garage door open.
Let the primer coat dry for 12-24 hours. Maintain adequate ventilation by keeping doors and windows open and avoid going near the floor while the primer coat cures. Wait a full day before resuming work on the floor for best results.
Mix one batch of each epoxy product immediately before application. Both epoxy primer and standard epoxy will come in 2 parts. Mix the two epoxy components for 5 minutes using a drill and stirring bit. Then, pour the mixture into a second bucket for another 5 minutes. Epoxy kits are pre-measured. Mix all of part A with all of part B to create the amount of epoxy listed. Most epoxy products (including most primers) have a “bucket life” of about 40 minutes, meaning that you must apply the mixture within this time window before it hardens.
Apply your first coat of epoxy with a ⁄4 inch (1.9 cm) nap roller. Begin in the corner of the room, and make your way toward the exit. Try to keep the roller wet at all times to ensure an even, thin coat. Move as quickly as you can without being sloppy. Epoxy has a short working time.
Wait 24 hours for your first coat to dry. Plan to wait a day before applying a second coat. While your first coat dries, ensure adequate ventilation during the drying process by keeping windows and doors open, if possible. Avoid going near the floor while the first coat cures. Curing time will vary slightly across epoxy products. Read and follow the manufacturer's directions for the product you select.
Check for cracks and holes before applying a second coat of epoxy. Examine your floor for any problems, including cracks, holes, or uneven surfaces that weren’t visible before. Seal any cracks with an epoxy crack filler and/or sand down uneven areas with fine 180-grit sandpaper. If you used sandpaper, do another run with your vacuum to remove any debris.
Wait 12-16 hours for the crack filler to dry if you used it. If you had to patch any new cracks or holes in your first coat of epoxy, wait at least half a day for the crack filler to dry before applying a second coat.
Apply a second coat of epoxy with an added non-skid solution. To help stop your floor from becoming too slippery, consider adding a commercial non-skid solution to your bucket of mixed epoxy according to the product's directions. Blend the solution well with a drill and stirring bit for around 5 minutes. Then apply your second coat, beginning in the corner and gradually moving toward the exit. In general, Add 3–4 fluid ounces (89–118 ml) of non-stick solution per every 1 gallon (3.8 l) of epoxy.
Let the second coat of epoxy dry for 24 hours. Avoid going near the floor while the second coat dries, ensuring the room is open and adequately ventilated. Give the floor at least a day to cure before walking on it or using it.
Comments
0 comment