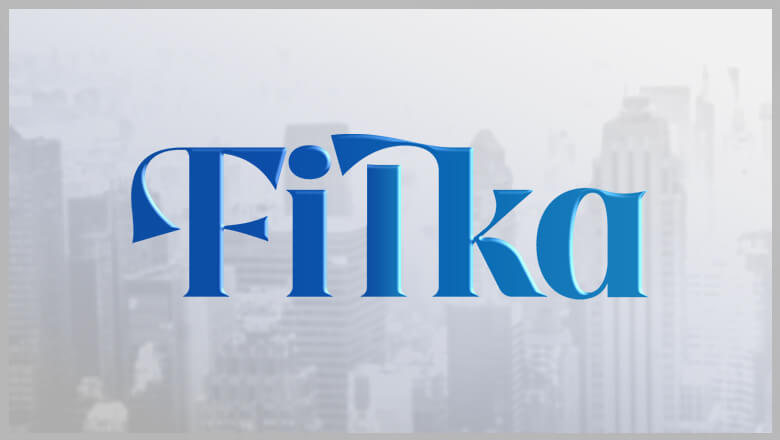
views
KOCHI: Two men from Kerala, a coconut artisan and a mechanical engineer, have come up with a product which might just be the next big thing in timber technology after rubber wood. They have developed a ‘coconut panel’. The panel, which looks physically similar to ordinary wood panel, is aimed at being a low-cost replacement for depleting forest woods like teak and rosewood.Both its makers, K V Ravindran and M Jesudas have been working in the field for more than 25 years now. Jesudas has been one of the pioneers in the rubber technology as well. He presented the technology to L&G, way back in the 1990’s.“Till the late 80’s, L&G was using imported wood for their projects including oil refineries, stadiums etc. But once I was able to convince them about the rubber wood, they replaced it all with rubber wood. The price of rubber wood has gone up dramatically now. It was a huge boost to the rubber planters. We are hoping the coconut panel will do the same to the coconut industry,” he says.One of the highlights of this technology is its eco-friendly angle. Lakhs of old and senile coconut palms are removed from farms every year by the Coconut Development Board, in order to enhance productivity. As of now only three districts are covered by the project.From these three districts alone, 6.47 lakhs coconut palms has been removed in the last two years. Once the project expands to the other districts, the number would naturally be much higher. But the bulk of this wood is wasted today. “All this wood which goes as waste now can be used to replace forest wood like teak and rosewood thereby saving a lot of our forests,” says T K Jose, Chairman of the Coconut Development Board.The technology used here is similar to rubber wood but, unlike the former, this technology has a few hurdles to pass before it reaches mass scale production. “In the case of rubber wood, we only had to convince the buyers, but here we have to educate the carpenter as well. The nature of the wood, the pins etc is such that without sufficient understanding the carpenter cannot use the wood. So here the promoter must develop the product as well. Once the product goes into the market, it will be introduced to the carpenters, who can then develop it," says Jesudas.The processing and the various chemical treatments have been done at several factories and research centres. For mass scale production these machines have to be imported and a factory to be set, this is apart from the land area of one hectare.“This product will be nonviable unless it is produced in mass scale. The factory alone will cost around 3 crore. We have submitted proposals to the KSIDC and the Coconut Development Board. Both of them have offered help, but they cannot take up the entire amount of 4 and a half crores. The CDB can give a maximum of `50 lakhs. The KSIDC has offered several subsidies and similar assistance. But we need a third party to take this forward as both of us lack funds,” says P N Ravindran.
Comments
0 comment